How Packaging Machine Repair Can Boost Your Production Output
How Packaging Machine Repair Can Boost Your Production Output
Blog Article
The Ultimate Guide to Packaging Equipment Repair: Keep Your Workflow Running Smoothly
Recognizing the complexities of packaging maker repair service is critical for keeping optimal performance and decreasing interruptions. Normal maintenance not just extends the life of these machines however likewise addresses typical issues that can restrain productivity.
Significance of Routine Maintenance
Regular maintenance of packaging devices is vital for ensuring optimal performance and durability. By executing an organized upkeep schedule, drivers can determine prospective concerns prior to they rise right into substantial problems. This aggressive strategy not only reduces downtime yet additionally expands the life-span of the equipment, inevitably causing decreased functional costs.
Normal assessments allow for the analysis of crucial parts such as sensors, belts, and seals. Attending to damage immediately stops unexpected failings that might interfere with manufacturing and cause costly fixings. Furthermore, routine maintenance helps ensure conformity with industry standards and laws, fostering a risk-free workplace.
Moreover, upkeep tasks such as cleaning, lubrication, and calibration significantly enhance machine performance. Enhanced efficiency translates to consistent item quality, which is important for keeping client fulfillment and brand name credibility. A well-maintained packaging maker operates at optimum speeds and lowers material waste, contributing to general productivity.
Usual Packaging Device Issues
Packaging machines, like any intricate equipment, can come across a variety of typical issues that might prevent their efficiency and performance - packaging machine repair. One prevalent trouble is irregular sealing, which can result in product perishing and wastage if plans are not effectively sealed. This frequently arises from misaligned parts or used sealing components
One more constant concern is mechanical jams, which can occur as a result of foreign items, worn components, or incorrect alignment. Jams can create hold-ups in manufacturing and increase downtime, inevitably impacting total efficiency. Furthermore, electronic breakdowns, such as failing in sensing units or control systems, can lead and disrupt procedures to unreliable dimensions or erratic machine behavior.
In addition, issues with product feed can likewise arise, where items may not be supplied to the packaging location consistently, causing interruptions. Lastly, wear and tear on rollers and belts can result in suboptimal performance, requiring immediate attention to avoid further damage.
Recognizing these common issues is vital for preserving the integrity of product packaging operations, guaranteeing that machinery runs smoothly and successfully, which in turn helps in meeting production targets and maintaining item top quality.

Fixing Methods
Efficient troubleshooting methods are crucial for immediately addressing problems that develop with product packaging machines. An organized method is essential for determining the source of malfunctions and decreasing downtime. Begin by gathering details concerning the symptoms observed; this might include unusual sounds, functional delays, or mistake codes presented on the machine's user interface.
Next, refer to the maker's handbook for repairing standards specific to the design in inquiry. This resource can give valuable understandings into typical problems and suggested diagnostic steps. Utilize visual evaluations to look for loosened links, worn belts, or misaligned parts, as these physical variables usually add to operational failures.
Carry out a procedure of elimination by testing individual equipment features. If a seal is not forming properly, analyze the securing system and temperature setups to establish if they meet functional specifications. Record each action taken and the results observed, as this can assist in future troubleshooting efforts.
Repair vs. Replacement Decisions
When encountered with devices malfunctions, choosing whether to change a packaging or repair equipment can be a complicated and vital option. This decision depends upon a number of key variables, including the age of the equipment, the degree of the damage, and the projected impact on functional effectiveness.
First of all, consider the device's age. Older devices may call for more regular repair services, bring about greater collective expenses that can exceed the investment in a new device. visit this site right here Furthermore, assess the seriousness of the breakdown. Minor concerns can usually be solved swiftly and economically, whereas considerable damages may demand a substantial economic commitment for repairs.
Functional downtime is an additional important consideration. Investing in a new maker that uses enhanced efficiency and reliability may be much more prudent if repairing the equipment will certainly cause extended delays. Think about the schedule of components; if replacement elements are difficult to come by, it may be a lot more tactical to change the equipment entirely.
Eventually, executing a cost-benefit evaluation that consists of both long-lasting and immediate ramifications will certainly aid in making a notified choice that lines up with this website your monetary restraints and operational objectives. (packaging machine repair)
Safety Nets for Durability
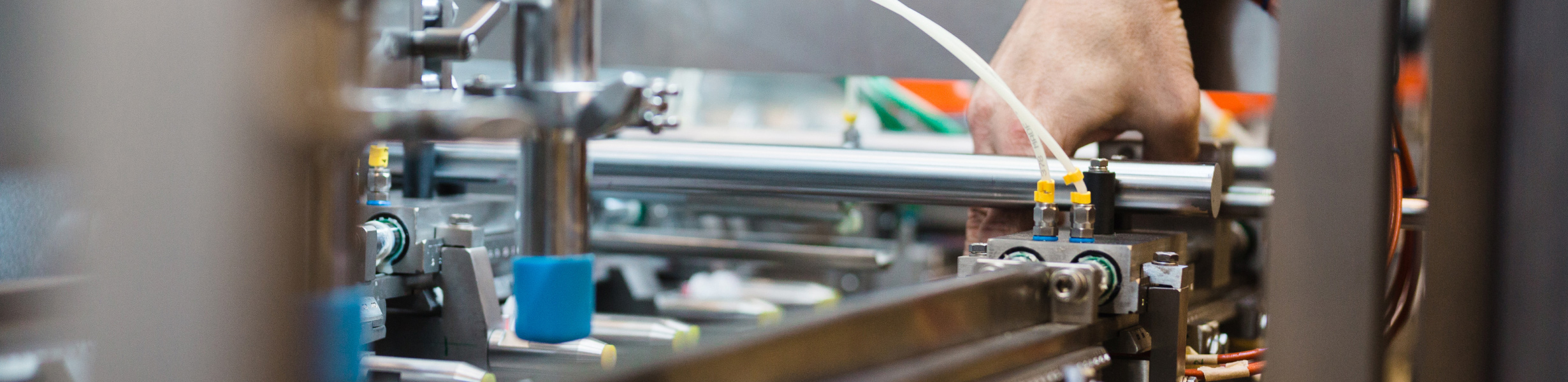
Secret preventative procedures consist of regular lubrication of relocating components, placement checks, and calibration of sensors and controls. Establishing a cleansing schedule to eliminate particles and impurities from equipment can considerably decrease deterioration (packaging machine repair). Additionally, monitoring functional specifications such as temperature and vibration can aid spot irregularities early on
Training staff to recognize indications of wear or malfunction is one more critical element of precautionary maintenance. Encouraging drivers with the understanding to carry out fundamental troubleshooting can cause quicker resolutions and lessen operational disturbances.
Documents of upkeep activities, including service records and assessment findings, promotes responsibility and helps with informed decision-making concerning replacements and repairs. By focusing on preventative procedures, services can guarantee their packaging equipments run at peak performance, inevitably resulting in enhanced productivity and lowered operational expenses.
Verdict
In conclusion, the efficient maintenance and repair of product packaging devices are critical for sustaining functional efficiency. By implementing precautionary measures, businesses can improve machine long life and guarantee uninterrupted performance in product packaging operations.
Understanding the complexities of product packaging device fixing is vital for Full Report maintaining ideal efficiency and lessening disturbances.Normal maintenance of packaging makers is important for making certain optimal efficiency and durability.Product packaging machines, like any complicated equipment, can run into a selection of usual problems that may impede their efficiency and efficiency. If repairing the device will certainly create long term delays, investing in a brand-new maker that supplies enhanced performance and reliability might be a lot more prudent.In verdict, the efficient upkeep and repair service of packaging makers are vital for sustaining operational performance.
Report this page